The respective characteristics of the drying capacity and method of the vertical roller mill and th
News Date:2020-08-25 14:18:28
As far as new dry-process cement is concerned, the requirements for the drying capacity of raw meal preparation are quite strict. The raw material moisture control index is <1%, and now cement factories generally control it within 0.5%. Raw material vertical grinding system, material grinding and drying are carried out internally. The material is extruded and ground to produce fine powder. Due to the extrusion force, centrifugal force and vibration, the material is brought to the periphery of the grinding disc, and then falls into the air ring. The high-temperature and high-speed (wind speed can reach 60-90m/s) vortex airflow in the air ring carries material particles into the vertical mill and the powder separator. Due to the effect of the retaining ring, there is only a small amount of large particles on the vertical abrasive bed. Relying on gravity, it passes through the wind ring and falls into the slag outlet of the vertical mill to be discharged; it enters the mill again through the external circulation conveying system of the mill (for vertical mills with external circulation) System, which accounts for about 40% of finished product output). Due to the straight cylindrical part of the vertical mill with a large cross section, the wind speed drops sharply, coupled with the centrifugal effect of the rotating cage of the dynamic classifier, the coarse particles settle; and the qualified raw material fine powder passes through the air duct, and is separated by a cyclone separator and a dust collector. Collect it. In this process, the temperature difference and speed difference between the powder and the drying hot air are very large, and it is suspended convective heat exchange, so the heat exchange rate is extremely fast, and the drying is completed in a very short time (less than 0.1s) process. Therefore, the drying capacity of the vertical mill is very large, and the moisture content of the three materials is easily controlled within 0.8%. Under the condition of only using the exhaust gas of the kiln tail preheater system, the comprehensive moisture content of ordinary human grinding materials can reach 7% to 8%.
Raw material drying method for final grinding system of roller press
In the final grinding system of the raw material roller press, the material grinding and drying processes are not carried out at the same time. The roller press squeezes and crushes the material to form a cake and discharges it. In the V-type separator, the cake exchanges heat with the hot air at the kiln tail. Although the material cake has been dispersed and refined by the impact and collision of the falling process, its particle group is still large. Because the hot air speed is small (the inlet and outlet wind speeds are 16-19m/s), the dispersion of the materials is small, and the heat exchange between the two is a mixed heat exchange method of heat conduction and a small amount of convection, so the finished material except the surface, The heat exchange effect is not good. In addition, 3 to 4 times the output of the finished product is added to the V-type powder separator to conduct centralized heat exchange with the hot exhaust gas from the kiln tail, occupying a large amount of effective heat and making the gas temperature significantly lower. The exhaust gas from the outlet of the V-type powder classifier carries fine particles into the secondary horizontal dynamic classifier for classification. The finished raw material enters the cyclone separator and the dust collector with the air flow and is collected; and the coarse powder returns to the roller press for squeezing. In the whole process, the temperature difference and speed difference between the raw meal powder and the hot gas are relatively small, so its heat exchange efficiency and drying capacity.
Much smaller than vertical mill system. Although the system designer distributes several hot air inlets in the tangential direction of the two-stage horizontal powder separator in an attempt to increase the effective heat capacity of the hot gas and increase the heat exchange rate, this measure will cause the powder separator to radially And the turbulence of the axial powder flow field is not good for powder selection, so it is of little significance.
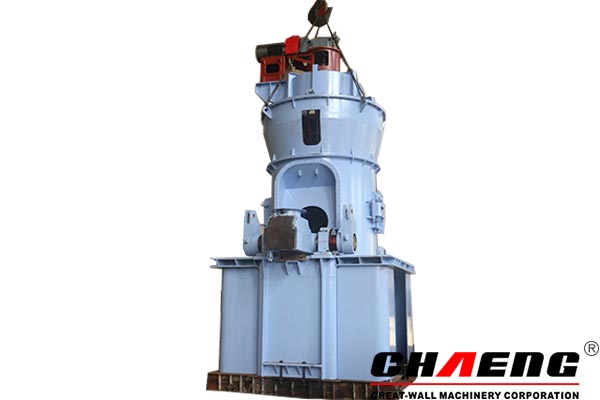
In fact, the particle size and dispersion of the cake into the V-type powder separator are extremely critical to the heat exchange effect. Because the hot gas temperature is higher here, if the fine particles in the cake can be fully dispersed in the hot gas, the heat exchange rate will be significantly increased. The dispersion degree of the material entering the V-type powder separator is more closely related to the compactness and the size of the cake. The greater the compactness and lumpiness of the cake, the worse the dispersion, and the more unfavorable the drying of the material. The compactness and lumpiness of the cake are not only related to the pressure of the roller press, the particle size of the material and its particle gradation, but also the comprehensive moisture of the raw meal and the cohesiveness of the raw meal. Therefore, reducing the comprehensive moisture content of the raw meal mixture is extremely important to give play to the power saving advantages of the final grinding system of the raw meal roller press.
According to the calculation of the heat balance of the roller press system, as well as the learned system configuration requirements and actual process control of each manufacturer, it is generally believed that if the high temperature exhaust gas (~3100C) of the firing system is used as the drying heat source, the roller press will end The comprehensive moisture content of the material in the grinding system should be controlled within 3%, so that the raw meal moisture content can be controlled within 0.8%; if the firing system has been equipped with a pure low-temperature waste heat power generation system, the general waste heat boiler outlet exhaust gas temperature is about 2200C, then The moisture should be controlled within 2.5%. If it is in the high-cold area and frozen soil ingredients are used, the roller press final grinding system should not be used.